[전기차]배터리 많이 넣으려면 차체 가벼워져야
알루미늄 등 대체 소재 주목..가격 아직 비싸
철강사 "고객 뺏길라"..초고강도 경량강판 개발
미국·유럽은 산학연 경량화 프로그램 활발
"국내도 부품사 참여한 경량화 프로그램 시도 필요"
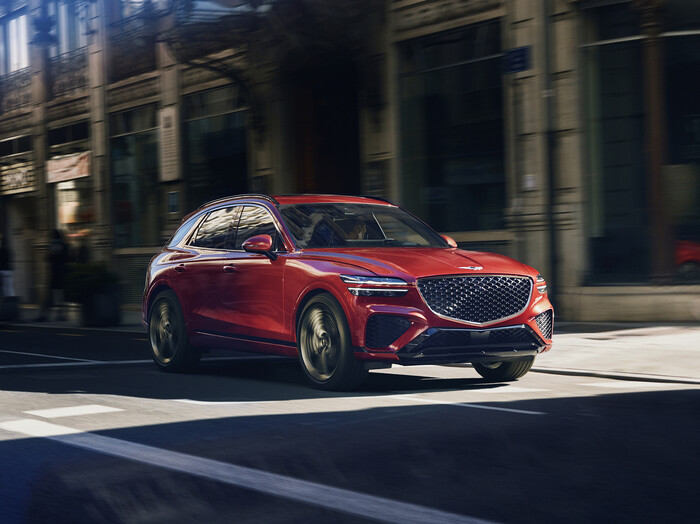
현대자동차의 고급브랜드 제네시스가 내놓은 전기차 지브이(GV)70은 기계식 주차장에 주차할 수 없다. 지브이70 전기차(20인치 휠) 중량은 2245㎏인데, 관련 규정에 따르면 중형 기계식주차장은 1850㎏, 대형 기계식주차장은 2200㎏ 이하 차량만 이용할 수 있다. 이 차량의 중량이 증가한 이유는 배터리 탓이다. 현대차 쪽은 “해당 차량은 고용량 배터리가 탑재되는 전기차의 특성상 내연기관 모델 대비 중량이 증가했다”고 밝혔다. 배터리를 많이 넣을수록 전비(1㎾h 당 달릴 수 있는 ㎞)가 높아지기 때문이다.
하지만 배터리를 너무 많이 넣으면 오히려 전비가 떨어진다. 전기버스가 이를 단적으로 보여준다. 전기버스(시내버스 기준) 배터리 용량은 290∼350㎾h에 달한다. 일반 승용차 배터리 용량(70∼80㎾h)의 3∼4배에 이르지만 전비는 1㎞대로 뚝 떨어진다. 무조건 배터리 용량을 늘리는 것이 능사가 아니다.
대신 완성차 업체들이 택한 방법은 차량 경량화다. 전기차가 주목받기 전부터 경량화는 자동차 업계의 화두였다. 한국자동차연구원에 따르면, 공차 중량 1500㎏인 차량 무게를 약 10% 줄이면 연비는 4~6% 향상된다. 동력 성능과 가속도가 향상되고 제동거리도 줄어든다. 가벼워진 차체가 충돌에너지를 줄여주면서 사고가 발생했을 때 차체 변형과 운전자, 승객 피해까지 줄일 수 있다. 차 강판을 연구하는 강연식 포스코 기술연구원 철강솔루션연구소 연구위원은 “경량화가 되면 주행거리를 늘리는 데 필요한 고가의 배터리 용량을 줄일 수 있다”며 “에너지 소비를 줄일 수 있어 친환경적인 면에서 유리하다”고 말했다.
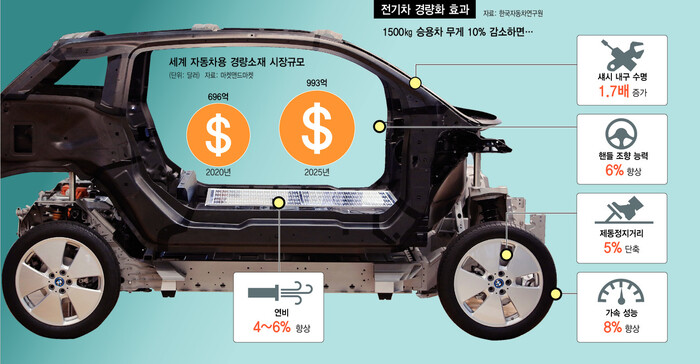
사실 그간 자동차 중량은 꾸준히 증가해왔다. 미국 자동차연구센터의 보고서를 보면 차량 중량은 1980년대부터 꾸준히 증가했다. 첨단 운전자 보조 시스템(ADAS)과 헤드업 디스플레이, 파노라마 선루프, 통풍시트 등 안전·편의사양(옵션)이 증가하고 있기 때문이다. 도요타 코롤라의 경우 공차 무게가 1992년 1090㎏에서 2013년 1255㎏, 2014년 1300㎏으로 증가했다.
이 보고서는 순수한 차체 무게의 경우 그간의 경량화 시도에도 불구하고 정체를 보인다고 설명한다. 1975년 1650㎏에 달했던 평균 차체 무게는 1980년대에 이르러 1200㎏까지 떨어졌지만 이후에도 1200㎏대를 유지하고 있다. 이현철 한국자동차연구원 광주본부 책임연구원은 각국의 충돌안전 규제 강화를 그 이유로 꼽는다. 이 책임연구원은 “미국, 유럽, 한국 등에서 충돌 시험을 할 때 부딪히는 상대 차량의 무게가 증가하고 충돌 속도가 늘어나는 등 꾸준한 규정 강화가 이뤄졌다. 차제 무게의 정체는 규제대응을 위한 구조 강화와 경량화에 의한 억제 효과가 동시에 작용한 결과로 볼 수 있다”고 말했다. 경량화로 줄어드는 중량이 구조 강화로 상쇄됐다는 것이다.
이런 규제 강화에도 안전규정을 지키면서도 차량을 가볍게 만들기 위한 노력은 지속되고 있다. 곧 다가올 전기차 주도의 친환경차 시장에서 경쟁력을 갖추려면 전비 향상이 필수이기 때문이다. 차량 경량화를 위한 방법으로는 크게 구조설계 개선, 신공법 개발, 경량 신소재 개발 등이 있다. 설계 개선은 차체 구조물을 최적화해 불필요한 요소를 제거하거나 소재 변경에 따른 최적 구조를 만들어내는 것을 말한다. 다수 제품을 일체화하고 통합하는 신공법 개발도 최근 주목받고 있다. 테슬라는 기가프레스라는 초대형 설비를 이용해 70여개로 구성된 후방 차체를 하나의 부품으로 제작하는 데 성공했다. 70여개 부품을 용접하고 이어 붙이는 데 들어가는 작은 부품을 없앤 만큼 경량화 효과를 볼 수 있다.
현대차그룹도 경량화 기술을 지속해서 발전시키고 있다. 최근 이 회사는 ‘핫스탬핑 공법’에 변화를 줬다. 핫스탬핑 공법은 기존 강판을 900℃ 이상의 고온으로 가열해 금형에 넣고 급속 냉각시키는 방식으로, 이 공법을 거친 강판은 가공 전과 비교해 5배 정도 강해진다. 올해 초 핫스탬핑 가열로의 온도를 기존보다 50℃ 이상 낮춘 특화 공법을 개발해 차체 강도를 20% 높이고 무게도 10% 줄였다.
설계 변경과 신공법 개발만큼이나 중요한 것이 신소재 개발이다. 컨설팅 회사 맥킨지에 따르면, 기존 자동차 차체의 대부분을 이루는 철강소재를 비철 경량금속과 엔지니어링 플라스틱 등으로 대체할 경우 최대 490㎏까지 무게를 줄일 수 있다. 철강을 대체할 소재 개발에는 유럽 업체들이 앞선 것으로 평가된다. 철강을 대체할 대표적인 소재로 떠오른 알루미늄을 유럽에서 더 쉽게 구할 수 있어서다. 유럽은 2000년대 초부터 자동차 업체, 소재·가공 업체, 대학·연구소가 컨소시엄을 이뤄 ‘에스엘시’(Super-Light-Car·SLC) 프로젝트를 운영하고 있다. 철강소재를 탈피해 알루미늄 등 다양한 경량소재를 적용하는 차체 경량화를 연구하고 있다. 그 결과 약 30%의 경량화를 달성할 수 있었다. 신소재의 단점도 있다. 바로 비싼 가격이다. 철강에 견줘 알루미늄은 약 2배, 탄소섬유 강화복합재(CFRP)는 약 10배 비싸다. 아직 철강을 완전히 대체하기에는 신소재들이 가격경쟁력에서 밀린다.
철강업체들도 경량화에 주력하고 있다. 자동차 강판은 철강업계의 주요 먹거리 가운데 하나다. 경량화 신소재의 가격이 하락하면서 보편화되면 철강업체들은 주고객인 자동차 회사를 잃을 수 있다. 그 전에 더 강하고 가벼운 자동차 강판을 내놓으려 하는 까닭이다. 미국은 철강업체들의 주도 아래 ‘미래철강차체’(Future Steel Vehicle·FSV) 프로그램을 운영하고 있다. 포드, 제너럴모터스(GM) 등 미국 완성차 업체뿐만 아니라 유럽 철강업체인 아르셀로미탈과 포스코 등 세계 철강 회사가 참여하고 있다. 이들이 자체 전기차용 실증을 진행한 결과 철강을 사용해도 2020년 안전기준 조건 아래 내연기관차 대비 약 35%의 경량화가 가능하다는 것을 검증했다.
포스코도 자체 경량화 기술 향상에 나서고 있다. 포스코는 2021년 초 자체 전기차 차체 모델인 ‘피비시-이브이’(PBC-EV)를 선보였다. 포스코가 개발한 초고강도 경량강판인 ‘기가스틸’을 45% 이상 적용해 기존 동일 크기의 내연기관 차량 대비 약 30%의 경량화를 달성했다. 포스코 설명에 따르면, 기가스틸은 알루미늄보다 3배 이상 강하고, 1㎟ 면적당 100㎏ 이상의 무게를 견딜 수 있다고 한다. 포스코 쪽은 ‘10원짜리만 한 쇳조각에 25톤(t) 트럭을 매달 수 있는 정도’라고 소개한다. 현대제철 역시 자체 경량소재를 적용한 ‘에이치(H)-솔루션 이브이(EV)’ 콘셉트카를 선보였다. 현대제철에 따르면, 이 차체는 동급 전기차와 비교해 약 9% 가볍고, 강도는 52% 증가했다.
국내 각 기업이 자체적으로 경량화에 힘쓰면서 일부 성과를 내고 있지만, 미국·유럽과 같이 산·학·연이 모여 경량화 기술을 연구하고 표준을 만들어야 한다고 전문가들은 조언한다. 이명규 서울대 교수(재료공학)는 “최대 자동차 시장인 미국과 유럽의 프로그램에 참여해 정보를 얻는 것도 중요하다”면서도 “국내에서도 현대자동차그룹과 포스코·현대제철, 대학, 연구소가 모여 한국형 차체 경량화 프로그램을 만들고, 연구역량이 부족한 협력사들을 참여시켜 시너지 효과를 낼 필요가 있다”고 말했다.
'자동차 > 국내 자동차' 카테고리의 다른 글
제네시스 'G90', 국내 최초 레벨3 자율주행차 된다 (0) | 2022.09.12 |
---|---|
[시승기] 쌍용차 토레스 T7 4WD '소비자의 눈은 매처럼 예리했다' (0) | 2022.09.10 |
[타봤어요]가족을 귀족처럼..'최고의 패밀리카' 카니발 하이리무진 (0) | 2022.08.31 |
기아 EV9은 이런 모습, 제로백 4.3초 대형 전기 SUV (0) | 2022.08.31 |
쌍용 전기차 '코란도 이모션', 생산은 재개했지만..전량 해외로 (0) | 2022.08.30 |